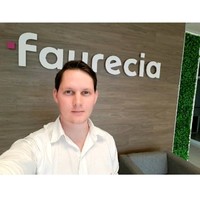
About Me
Name:
Michael Coetzee
Email:
Michaelcoetzee.ie@gmail
Phone:
(+27)-817-661-126
Date Of Birth:
11 September 1993
Address:
67 Hampshire Street Port Elizabeth Eastern Cape
Nationality:
South Africa
I am seeking the opportunity to apply myself to an industrial engineering / production manager position to enable me to capitalize on both my educational and professional experience whilst allowing me to progress in my career. I wish to secure the position to develop my knowledge as an industrial engineer with keen interest in systems engineering and production management.
I have gained valuable knowledge in production systems working as the plant FES & P (Lean manager). Key achievements including rapid learning of the FES (Faurecia Excellence System), which involved implementation of best practices throughout all functions from HR, production, quality, maintenance and engineering, production control and logistics. These deployments were subjected to routine audits from corporate level to adhere to strict standards for each deployed system. Addition to FES I am responsible for the plant’s productivity looking at the labour and machine efficiencies. This included driving Hoshin/Jishuken activities to improve the direct labour efficiencies through line balancing techniques and potential of productivity analysis.
I have gained insight through various continuous improvement projects which I have developed a good understanding of lean principles. I believe I am dynamic, team spirited, and performance driven in continuous improvement profession, whose primary role is to identify, lead and execute continuous improvement strategies through theory of constrains, lean and six Sigma techniques within the organization.
I believe I am highly committed, work well in teams and have keen interest to assist coordinators involved in a variety of operation’s functions to gain experience and a better understanding of the field of industrial engineering.
Yours sincerely
Michael Coetzee
Services
Process Optimisaiton
Line Balancing
Digitization Leader
Management
Resume
Experience :
FAURECIA INTERIOR SYSTEMS
May 2019 to 2021
Industrialization Program Manager
Accountable for the launch of the various programmes including VW 270 PA, VW Amarok, Ford Ranger.
- INDUSTRIAL DEVELOPMENT
- Full ownership of all Industrial Development activities of the Program:
- Responsible for the work packages execution for the Industrial Development of the Program at the Plant: industrial footprint, Plant equipment selection (new / reuse / share), Plant layout, MIFD / MIFA, industrial trials …
- Responsible for the launch planning and budget from definition till execution
- Participate in the development of Make or Buy strategy in accordance with Purchasing, Program and Plant(s)
- Starting from phase 3, be responsible for HSE and ergonomic convergence in the Plant
- Define the Industrial Development support team required resources in terms of workload, competencies and profiles
- Manage the Industrial Development support team to ensure Industrial Development and Plant launch readiness by conducting reviews, assigning tasks, driving accountability and preparing launch related staffing and training plans
- PRODUCTION LAUNCH
- Management of launch activities at the Plant:
- Complete the Industrial Development support team with required resources (internal / external) in terms of workload, competencies and profiles
- Liaise with UAPs and PC&Ls to plan production related runs / trials
- Coordinate the installation and launch of production equipment and tooling
- Support the production during the ramp-up after the handover.
FAURECIA INTERIOR SYSTEMS
May 2018 to 2019
Plant FES & P (Lean Manager)
1. At Plant level, provide FES expertise (HSE, Quality, EE, PC&L and Production system) based on 11 lean manufacturing principles to contribute to achieve operational business targets
• Follow up of the FES deployment plan, to support the Plant Improvement Plan (PIP) execution.
• Provide, according to the needs, FES knowledge and skills to the plant team through training, coaching and education.
• Participle to FES Principles in Programs from design stage (lean process design, MIFD, validation of Equipment design, cardboard workshop activities, Standardized Work ,OHP, process layout, packaging,
• Etc…)
2. Contribute to the Plant MOD cost budget construction & achievement, through efficient “MOD cost management” & “MOD cost improvement plan”.
• MOD Cost Management at Plant level:
• Ensure routing and coefficient data management methodology is correctly applied and respected, for direct standard and actual Labor cost accuracy.
• Ensure DLE/DLP tracking process linked with the DL cost % results
• MOD cost improvement:
• Support SW construction and adherence, development of OHP (primarily GL and Supervisor role and routines), as the main foundations to achieve high levels of operational performance.
• Support the implementation of FES improvement tools for production reliability, change over Standards (flexibility), reduction of Line stoppages, Line balancing, and overall MOD efficiency to ensure identification of MOD “Productivity Potential.
• Contribute to the lead time reduction though the implementation of continuous flow, layout optimization, pull-system and speed up flows works.
3. Support FES network Animation in the plant
• Contribute to deploy FES culture at Supervisors & GAP Leader level
• Propose and promote best practices within the Plant (FES Network)
• Participate in Division level workshops to test the new” lean concept” or advanced tools.
Federal Mougal Motor Parts
May 2017 to April 2018
Industrial Engineer
Value Stream engineer which included integration into a cross functional role, executing constraint management across all departments in the value stream and driving technical/ productivity savings opportunities..
Key objectives included:
– Achieving customer fill rates by increasing throughput through various improvement projects.
– Increase pieces per man hour by focusing on system constraints, determining highest non-productive time, actioning solutions to increase up-time performance, availability and quality.
– Reduce inventory and Wip through square management, identification and implementation of
pull systems.
– Second level Pareto analysis on non-productive minutes to drive process improvement projects.
– Lead and execute technical savings opportunities through material reduction, labor flexing, cross
functional training, cycle time reduction through; combining, reducing and removing.
Key Deliverables included:
– Achieving technical savings budget of 3m pa.
– Implementing and driving constraint management reducing inventory by 27% in the value stream.
– Increasing Pieces per man hour
– Designing a high volume cell to increase throughput and customer fill rates
Autovest
January 2017 to May 2017
Quality Co-ordinator
Mainly involved in managing the QMS system, managing the quality inspectors and ensuring strict incoming/ outgoing quality standards in process to meet customer requirements
-Maintaining and serving as an administrator of the Quality Management System
-Ensuring that a document control procedure is adopted to approve, review and update all changes to critical documents within the scope of the QMS
-Assisting departmental managers in setting and documenting workflow / procedures for all departments
-Ensuring the promotion of awareness of the SHEQ Management System throughout the organization.
-Ensuring that all new staff are inducted into the requirements of the QMS related to their own roles and responsibilities.
-Coordinate corrective actions in response to internal non-conformances, customer issues, and system weaknesses.
-Analyze customer complaint, internal non-conforming products & process issues and make recommendations for improvements.
-Monitor resolution of corrective actions from audits and non-conformities and report status.
-Coordinate and participate in conducting SHEQ audits (ISO), document results, and report statusa.
Education :
Nelson Mandela Business School
2019 - 2019
Masters in Business Administration
Currently studying towards a master’s in business administration in 2020 to develop leadership skills and expertise in all functions of business. Even the most compelling and visionary ideas remain dormant without leaders to give them life.
Nelson Mandela Business School
2019 - 2019
Post Degree In Business Administration
The PDBA provides individuals with the opportunity to attain a world-class business education by developing a broader and deeper understanding of business management and leadership, through theory and practical application.
Nelson Mandela University
2018 to 2018
Btech Industrial Engineering
Achieved my degree in industrial engineering to further my capabilities as an industrial engineer. Modules completed include project engineering, research, system dynamics, information systems for management, logistics engineering, quality assurance, production techniques and entrepreneurship.
Nelson Mandela University
2013 to 2016
Industrial Engineering Diploma
My Skill
My Professional Strengths
“Good is the enemy of great” – Jim Collins, this statement solely drives my curiosity to understand what is needed to change any instance, be it personal goals or professional goals to “great” or exceptional.
Language skills
You will begin to realise why this exercise is called the Dickens Pattern with reference to the ghost showing Scrooge some different futures as you notice that the idea of this exercise is to hypnotize yourself to be aware of two very real possibilities for your future. Two distinct pathways
Knowledge
Progressing in my career I have had the benefit of learning from some of the best mentors and companies in the industry. Identifying skills to master and develop core capabilities to lead and execute various tasks through experience or critical thinking.
- Jishuken
- Hoshin
- Non-TRS and OEE
- Line Balancing
- Creative problem solving
- QRCI
- Industrial design and method study
- Block diagram, Ishikawa, 8D
- Cultivate a design sense
- Right balance of tools
- Approach every new skill
- Good business management